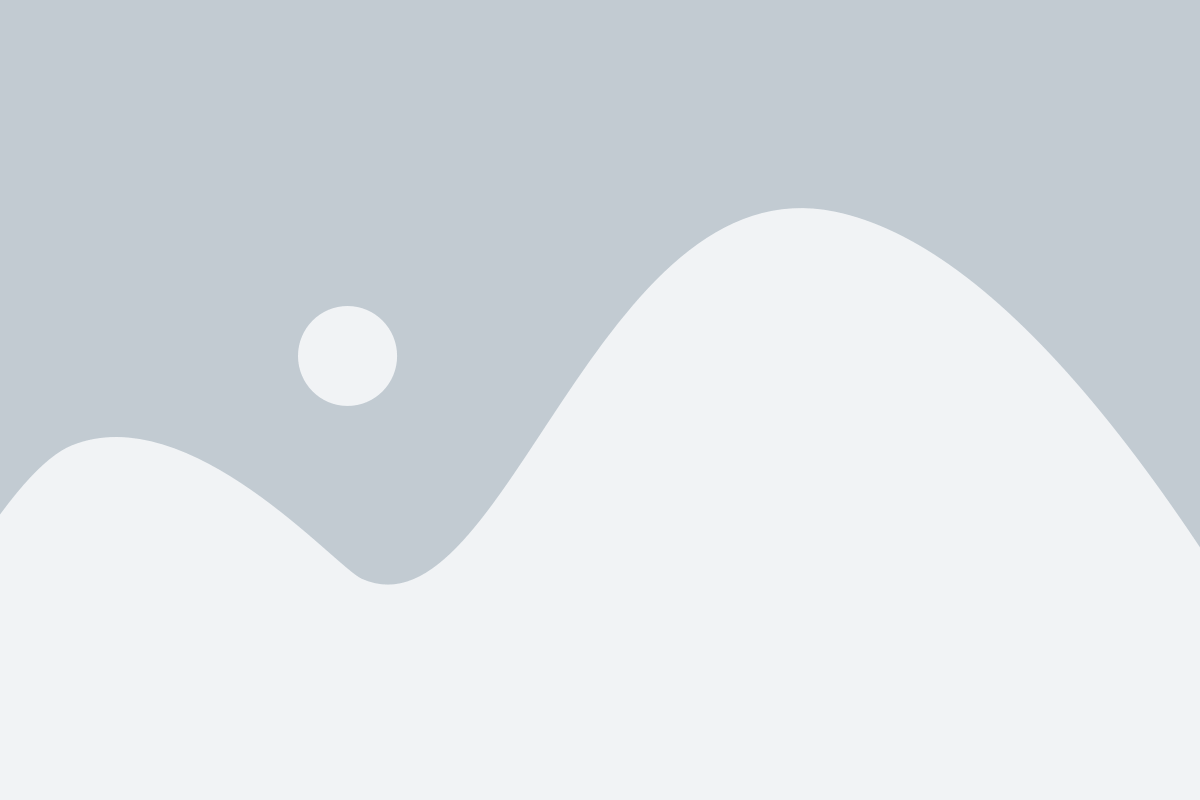
The Role of IoT in Enhancing Predictive Maintenance Strategies
In today's rapidly evolving industrial landscape, businesses are constantly seeking ways to optimize operations, reduce costs, and enhance efficiency. One of the most impactful technologies in achieving these goals is the Internet of Things (IoT). By integrating IoT solutions with predictive maintenance strategies, companies can proactively manage equipment and machinery predictive maintenance, ultimately leading to significant cost savings, reduced downtime, and improved operational performance.
What is Predictive Maintenance?
Predictive maintenance (PdM) refers to the practice of using data-driven insights to predict when equipment is likely to fail, enabling businesses to perform maintenance tasks just before a failure occurs. This approach helps avoid unnecessary repairs and reduces unplanned downtime. Traditionally, maintenance has been reactive (fixing equipment after it breaks) or based on scheduled intervals (performing maintenance regardless of the machine's actual condition). Predictive maintenance shifts the focus to understanding the condition of equipment in real time and predicting failures before they happen.
How IoT Enhances Predictive Maintenance
IoT plays a critical role in predictive maintenance by enabling continuous monitoring and providing real-time data from equipment. IoT sensors are embedded in machinery, collecting data on temperature, vibration, pressure, humidity, and more. This data is then transmitted to cloud platforms where it can be analyzed, providing valuable insights for maintenance teams. Here's how IoT enhances predictive maintenance strategies:
1. Real-Time Monitoring and Data Collection
IoT sensors gather real-time data from machines and equipment. This constant stream of information allows businesses to monitor their assets continuously, ensuring that any changes in performance are detected early. Unlike traditional maintenance approaches, which rely on periodic checks, IoT-enabled monitoring ensures that maintenance teams are always in the know about equipment status.
2. Data-Driven Insights for Better Decision Making
IoT systems collect vast amounts of data, which can be analyzed using advanced analytics and machine learning algorithms. By processing this data, businesses can uncover patterns and trends in equipment behavior that indicate wear and tear, mechanical stress, or impending failure. These insights allow maintenance teams to make informed decisions on when and where to focus their efforts, minimizing downtime and preventing costly repairs.
3. Improved Equipment Lifespan
With continuous monitoring, IoT sensors can identify minor issues before they escalate into significant failures. Early detection allows for timely interventions, which can extend the lifespan of equipment. By addressing small issues early, businesses can reduce the frequency of major repairs and replacements, which can be expensive and time-consuming.
4. Predictive Analytics and Machine Learning
IoT-enabled predictive maintenance systems use machine learning algorithms to predict failures based on historical data and real-time sensor readings. These systems can analyze data from multiple machines and even predict the remaining useful life (RUL) of equipment. By forecasting when a machine is likely to fail, maintenance teams can plan interventions accordingly, reducing the likelihood of unexpected downtime and increasing operational efficiency.
5. Cost Savings and Efficiency Gains
The primary benefit of predictive maintenance powered by IoT is the potential for significant cost savings. By only performing maintenance when necessary, companies can reduce the costs associated with unnecessary repairs, replacement parts, and labor. Additionally, minimizing unplanned downtime ensures that operations continue smoothly, maximizing productivity.
6. Remote Monitoring and Support
IoT allows for remote monitoring of equipment, which is especially valuable in industries with large, geographically dispersed assets, such as oil and gas, transportation, and manufacturing. Maintenance teams can monitor equipment performance from a central location and even receive alerts when an issue is detected. In some cases, remote diagnostics and troubleshooting can be performed, reducing the need for technicians to visit sites physically.
Conclusion
The integration of IoT in predictive maintenance strategies marks a revolutionary shift in how businesses approach asset management. With continuous data collection, advanced analytics, and machine learning, IoT enables organizations to predict failures, optimize maintenance schedules, and reduce costs. As industries continue to embrace the digital transformation, IoT will remain a key player in driving efficiency and performance in predictive maintenance strategies.
By leveraging IoT technology, companies can stay ahead of potential failures, ensuring their equipment operates at peak performance and avoiding costly downtime. The future of predictive maintenance is here, and IoT is at the heart of it.